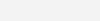
FLOW PROMOTION LINING
Thermoplastics as Flow Promotion Linings
Polystone ® M + G15 is a family of polymer alloys and a low friction material that solve the problems of friction, wear and the flow of material across many industry sectors. An exceptional low friction material surface, outstanding wear resistance, high impact strength, excellent chemical resistance and superior performance in demanding applications characterize the key properties of the product.
Compared to steel, Polystone ® M + G15 has considerable economic benefits:
- Lower cost: The cost for lining an existing bin with Polystone ® M + G15 is only about one third of the cost for construction steel.
- Lower weight: For example, the refurbishment of a 200m Polystone ® M + G15 would achieve a reduction in weight of almost three tons compared to the standard method of welding steel sheets. Polystone ® M + G15 reduces the load on the structure and makes installation work much simpler.
- Longer life span: Conventional construction steel. In the sand-slurry wear test, at 150 (S235JR).
UNDERSTANDING FLOW PROBLEMS
Cohesive bulk materials do not flow easily e.g. in chutes and hoppers. They stick to the walls and will affect productivity. Moisture, storage time at rest and other factors affect the flow properties of the bulk material. Arching and rat holes are two common problems that usually develop when either the outlet is too small or when the hopper lining material does not promote flow due to shallow wall angles or rough wall conditions caused by corrosion.
Segregation will occur if material discharges from the bin in a funnel flow pattern. The centre portion of the bin empties first, followed by the material along the walls. This creates segregation because as the bin was loaded the finer particles collect in the centre of the bin under the charging point while the coarse particles roll to the periphery of the bin along the walls. In order to remix the material during discharge a mass flow pattern is required to minimize or eliminate segregation. Polystone ® M + G15 reduces the friction between the bulk material and the walls of the hopper and thus allows the material to flow out and to empty the hopper completely.
RESULTS OF FLOW PROBLEMS
- Delayed start-up – increased cost
- Limited live storage
- Spontaneous combustion (stagnant coal)
- Quality compromised
- Segregation
- Silo vibrating or shaking
- Silo structural failure
- Wear of equipment
- Process out-of control
- Operator intervention
Funnel flow is referred to as first-in last-out and is ideal for free flowing bulk materials. The bulk material discharges from the bin through a small channel in the centre of the bin above the outlet and the material along the wall remains stationary until the end. Mass flow is referred to as first-in first-out and is required for cohesive bulk materials. It is defined as all the material is in motion whenever any is withdrawn.
In order to create mass flow, the hopper walls must be smooth and steep enough and the outlet must be large enough to prevent arching.